Year of implementation: 2022
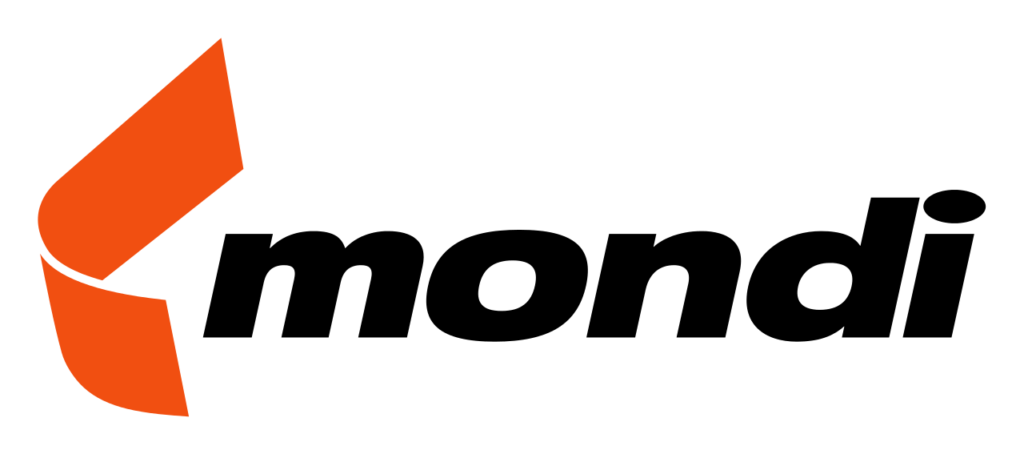
Mondi Group
Industry: Paper industry
Country: Global solution
Customer’s website: mondigroup.com
Key benefits:
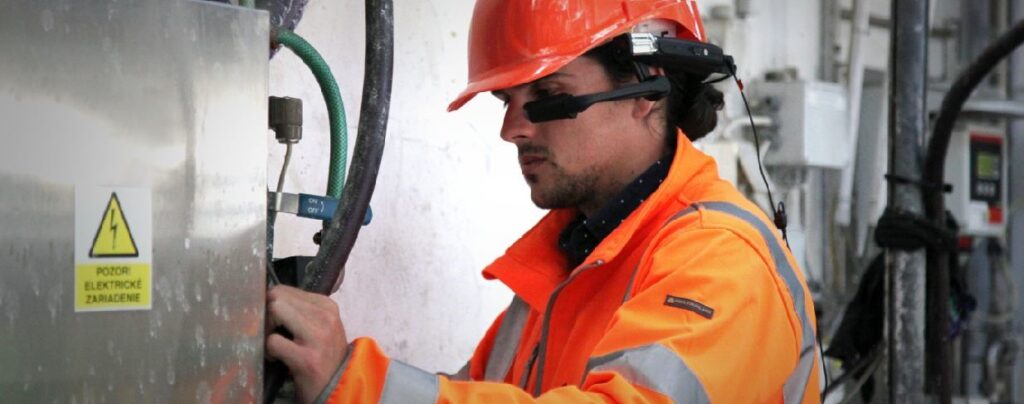
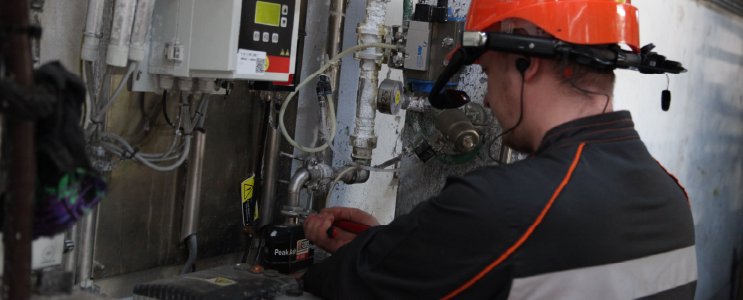
Smart glasses with augmented reality as key to improve the quality of maintenance in paper industry
The smart glasses technology can also be used in the harsh conditions in the paper industry with high noise and dust levels. Mondi, the global leader in packaging and paper, has a great deal of positive experience to share.
Since it was established in the 1960s, Mondi, originally a South African company, has been a prominent player in the paper industry. Today, Mondi is a global leader in its field and owns over 100 production facilities in more than 30 countries, with key plants in Europe, Africa and North America.
AYES and Mondi started collaborating through the Slovak production facility in Ružomberok. Its management was looking for a solution that would improve the working conditions of the maintenance team and increase the efficiency, speed and quality of processes. The solution presented itself in the form of RealWear smart glasses in combination with the TeamViewer Frontline xAssist software and the superior service support and consultancy provided by the AYES technical team. Thanks to this positive experience, the selected solution is now being implemented as a global project at all the group’s production facilities.
A handy partner for harsh conditions
Previously, maintenance workers at Mondi performed routine equipment maintenance based on initial training and instructions provided by the manufacturer of the given equipment. However, the problem was the inconsistency of the performed maintenance by individual team members, often also accompanied by difficult and lengthy communication with foreign specialists for the given technology in case there was an accident. Consequently, Mondi needed to make the processes more efficient and standardized. Samuel Dvorštiak, a Digital Specialist at the Slovak plant who is responsible for the implementation of smart glasses, adds: “Some work of the maintenance team could not be performed or it was done in a very complicated and a bit amateurish way using videos made with mobile phones. The videos were then downloaded to computers and sent with comments by e mail, which was a bit clumsy. Thanks to smart glasses, the whole process is much more professional.”
In the end, the combination of RealWear smart glasses and the TeamViewer Frontline xAssist software proved to be ideal for the production of packaging and paper, which has a high level of noise and dust. There are several reasons for it.
The RealWear glasses are a cutting-edge hands-free technology for harsh industrial conditions. The voiceoperated operating system with speech recognition that works in noisy environments, soundproof microphones with clear sound quality also at 100 dB of background noise, integrated speakers and 3.5 mm audio jack to connect the glasses to a headset were exactly what Mondi needed. In combination with high resolution display and excellent visibility, it was an easy choice. The mandatory wearing of protective hardhats was not a problem either. The glasses are designed to be worn with hardhats, reinforced caps and protective goggles.
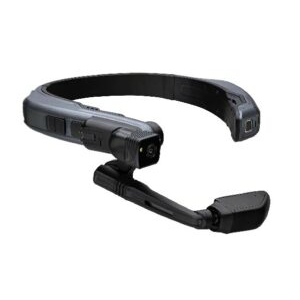
Smart glasses RealWear Navigator™ 500 are the world´s leading hands-free technology in the industry.
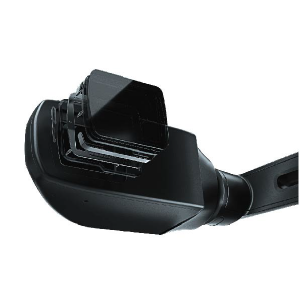
The display with excellent visibility and high resolution acts as a voice-controlled tablet for the user.
Remote support with augmented reality
The TeamViewer Frontline xAssist software helps Mondi speed up response time if repairs are needed and saves money that would otherwise be spent to send a specialist from the technology supplier. If an accident happens and production is stalled, the financial loss can be substantial. Therefore, repairs in case of an accident are time-critical. Samuel Dvorštiak adds: “The possibility to quickly establish connection between a technical expert and our people is a big advantage. Thanks to smart glasses the expert operating remotely sees exactly what the technicians at our plant see and can provide support without the need to come to the plant. All this with real-time picture and sound transmission.”
A reliable system with high-quality support
The smart glasses technology is gradually being implemented at multiple Mondi’s production sites around the world. AYES provides both technical and user support to all of them. Peter Puck, the Category Manager Technical Procurement, is responsible for a successful global implementation. He says: “I´m really satisfied with the professional and proactive support from the AYES team. They provide us with all the service that we need, from the initial training and support in the first stages of the implementation to the help with integrating of documents into the smart glasses. Therefore, we are planning to continue to expand our cooperation.”
“Some work of the maintenance team could not be performed or it was done in a very complicated and a bit amateurish way using videos made with mobile phones. The videos were then downloaded to computers and sent with comments by e-mail, which was a bit clumsy. Thanks to smart glasses, the whole process is much more professional.“
Samuel Dvorštiak
Digital Specialist
Mondi SCP, Slovakia
“We are really satisfied with the professional and proactive support from the AYES team. They provide us with all the service that we need, from the initial training and support in the first stages of the implementation to the help with integrating of documents into the smart glasses. Therefore, we are planning to continue to expand our cooperation.”
Peter Puck
Category Manager Technical Procurement
Mondi Group, Rakousko